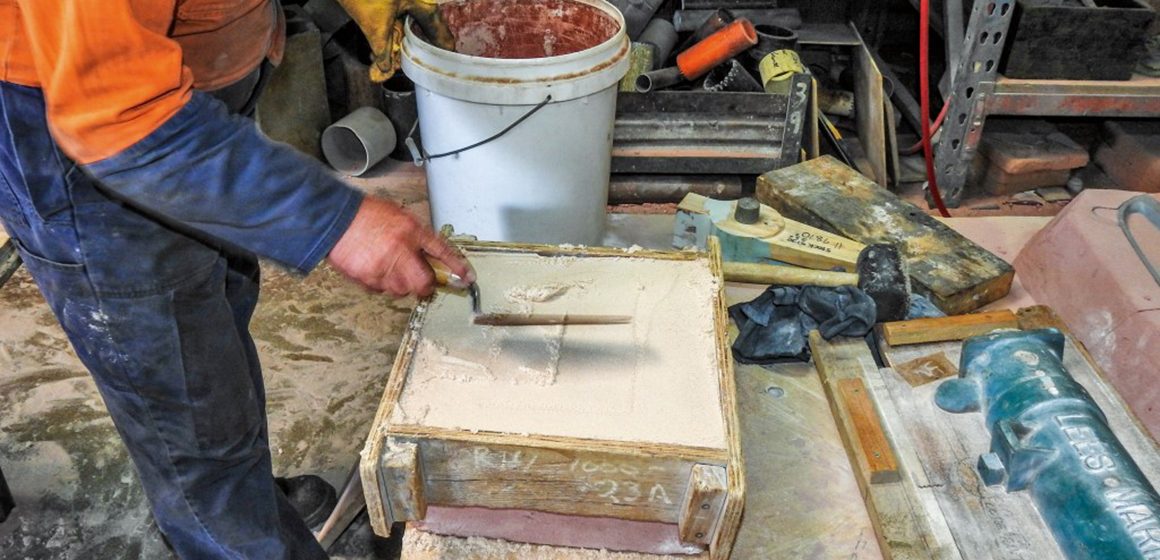
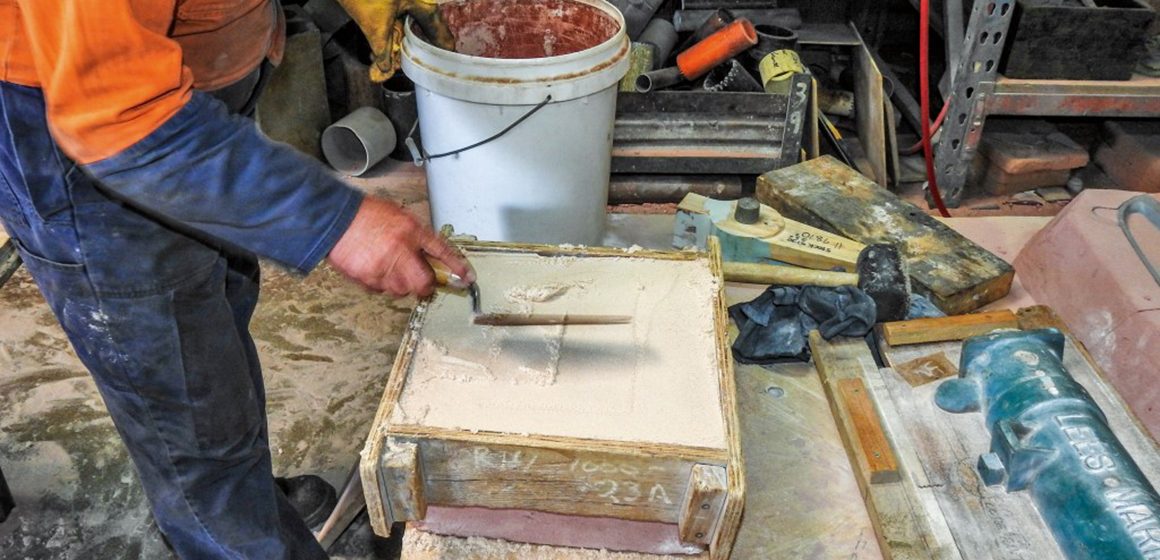
If you’ve lost or broken one of your boat’s rare bronze fittings, don’t despair. Sourcing a replacement is easier than you think – you just need to visit your local foundry. Story by Norman Holtzhausen.
Every owner of a historic vessel understands that part of their charm lies in the beautiful bronze fittings – they always add character to a boat. And bronze is a great material for these fittings since it has few corrosion issues and is strong enough to form propellers, shaft struts and rudder pintles.
WHAT IS BRONZE, EXACTLY?
Well, there are different types of bronze.
Bronze is an alloy of copper and small amounts of another metal. Phosphor bronze has less than 1% each of tin and phosphorus added and is known for its low-friction surfaces and high fatigue-resistance.
Nickel Aluminium Bronze (Nibral) contains about 10% aluminium and about 5% nickel. It’s more rigid with higher strength and better corrosion resistance than conventional bronze. Nibral is commonly used for high-performance boat propellers.
Other variations include silicon bronze, cupronickel and even nickel brass which has a silver appearance. The exact composition of bronze to be used depends on the desired characteristics of the finished product, although for most deck fittings this is not likely to be critical.
Note that bronze is different to brass, which is an alloy of copper and zinc and has considerably less strength and corrosion resistance.
In our modern throw-away society, how do you replace a 20-, 30- or even 100-year-old fitting that’s been lost? Bronze fittings usually outlast the surrounding woodwork on older boats – items often disappear only because the underlying structure fails, rather than the fitting itself.
Older items are almost certainly no longer being made, at least not in the same style. You could troll through second-hand stores or look online to find something the same. Alternatively, you may be forced to replace all the fittings to achieve a consistent style throughout.
But there is a simpler option – casting an exact copy of the component. And somewhat surprisingly, this may also turn out to be no more expensive than an off-the-shelf bronze fitting, assuming you can even find a chandler that still stocks it. As long as you have (or can create) a sample, a copy can be made.
And so I went off to talk to Mike Rees (Mike Rees Castings) who has been in the business for over 40 years and has been based at his Glenfield location for the past 25 years.
Rees says theirs is a centuries-old industry, which pre-dates mankind’s ability to machine metal. Over the last few centuries though, the art of creating the casting has become just the first step of the process – today the raw component is finished off with specialist tools. It’s smoothed and polished and finemachined for critical surfaces and dimensions.
In many respects the sand-casting process has changed very little since the Bronze Age, apart from a slight tweak in terms of the sand used. The traditional hot metal casting system used a moulding material referred to as greensand – basically an organic mixture of sand, clay and water.
Today Rees uses the latest resin-based sand mixture, produced on-demand by an automatic mixer on site. This sets within a few minutes which means the turnaround time for each casting is a fraction of that required for the greensand system. And because it doesn’t contain water it doesn’t cool the metal as quickly as greensand. Slower cooling delivers more consistent results.
Every casting has a riser section down which the molten metal is poured. It’s eventually cut from the finished part and remains molten for longer than the main body of the casting. That pool of molten metal allows the body of the object to ‘pull back’ some more material as it cools and contracts slightly, creating a solid casting without voids.
Because the thermal contraction is typically about 1.5% in bronze, it does result in the casting always being fractionally smaller than the original. In most cases this is not discernible, but Rees says it is sometimes a problem with lead for yacht builders who design keel bulbs to a very precise size and weight. They are understandably frustrated when the final casting is fractionally undersize.
HOW IT’S MADE
The first stage of the casting process, explains Rees, is sourcing the object to be moulded. This could be an original part that you want duplicated, or a wooden or plastic carving of the desired shape. It forms the pattern for creating the mould.
For propellers the pattern typically comprises just a single blade and the hub. The blade is indexed three, four or even five times around the hub to create the full prop and its required number of blades.
Next, a batch of resin sand is machine-mixed and the first half of the mould created. The sand is packed around the pattern (which is dusted with a mould release agent to prevent it sticking to the sand). Excess sand is smoothed off and the object is removed. Indexing points are created to ensure the second half of the mould will line up correctly with the first part. Any imperfections in the mould are easy to correct at this stage.
Once the resin has set the object is re-inserted, with more mould release agent, the second half of the mould is filled with sand. This is again packed down and smoothed off, and again allowed to set. The top half is eased off, the original part or pattern is removed, and any imperfections sorted out. Finally, the riser channels are created down which the molten metal will be poured. At last the mould is ready to be cast.
Molten bronze emerges from the furnace at around 1200°C and is poured into the mould. As it cools the metal contracts and the still-molten pool at the top of the riser takes on a concave shape. Depending on the size the casting is left for up to an hour to solidify. After that the sand is removed and the raw casting appears. It has a rough surface and the riser is cut off and the edges cleaned.
Now the casting goes through a finishing process. For most fittings this is a simple smoothing and polishing. With propellers, though, the hub is machined to match the required shaft size and taper, the blades polished and balanced, and a keyway cut. This process is generally tackled by one of the specialist propeller engineering firms.
Rees says that the casting industry has lost a lot of business in recent years to CNC milling machines but is adamant the casting process holds advantages. A propeller, for example, can take a CNC machine up to 24 hours to machine, whereas a casting and finishing process can complete it in a fraction of that time.
CNC machines also work on one item at a time and are not suited to a production run of multiple copies. CNC creates a huge amount of waste: a solid block of material is required equal to the largest dimension of the finished product. Up to 95% of the original material may be removed in a CNC process. By contrast there is very little waste from casting, and any extra material can be recycled into the next casting.
The cost of having a custom casting is also surprising, given that costs are directly related to size and weight of a component rather than its complexity. To have a part CNC-machined you first need a digital pattern, which can take many hours to develop. By contrast, if you have an existing example of an object you can readily duplicate this through the casting process with minimal effort and cost.
Rees’ company also makes castings with other non-ferrous metals such as aluminium and lead. Larger-scale projects the company has tackled include keel bulbs up to 15 tonnes, and propellers up to 1.5m in diameter.
If you need a replacement part, or even need a unique shape moulded in metal, give him a call.