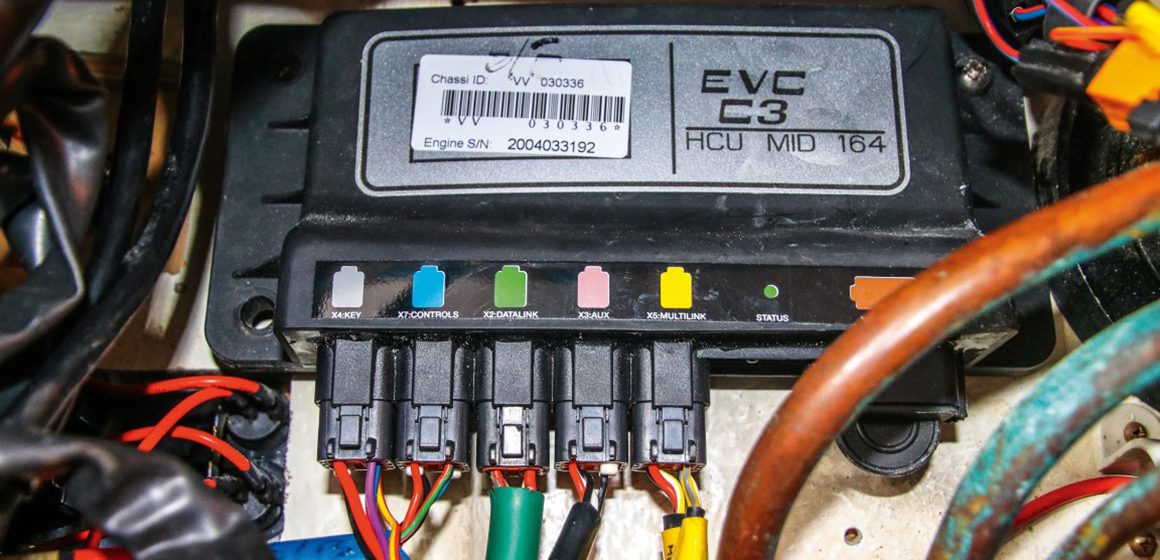
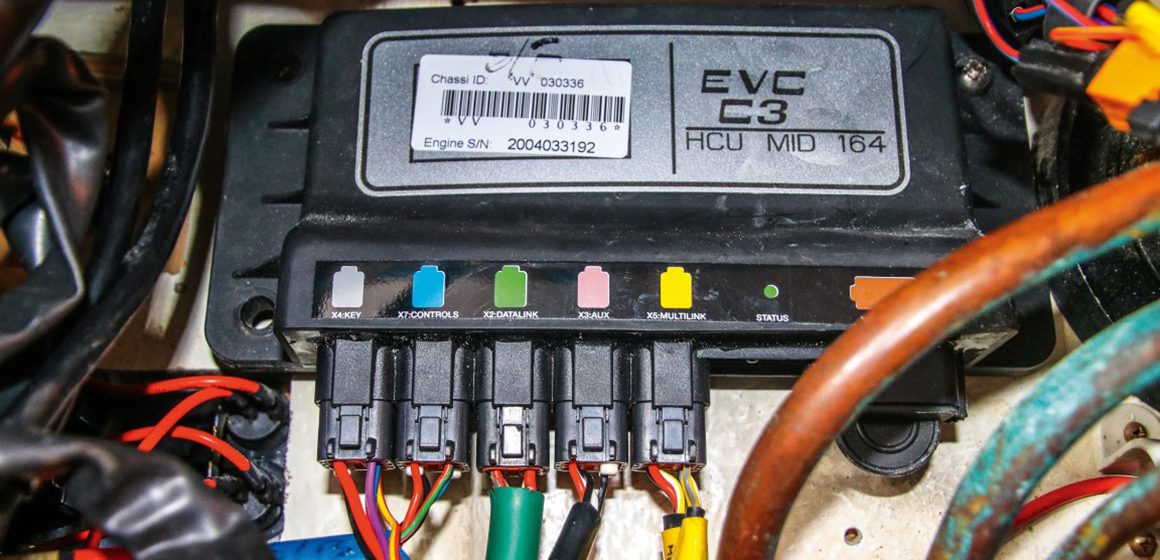
Everything seems to be controlled by a computer these days, including boat engines. Those of us with more than a few decades under our belt will remember the days when starting up an engine – diesel or petrol – required a few manual steps. Not any more, writes Norman Holtzhausen.
When did you last have to use the choke lever before cranking the engine, and push it back slowly as the engine warmed up? With diesel engines, do you remember holding a button for about 10 seconds to heat the glow plugs before cranking?
In either case the engine would usually fire up in a cloud of smoke, and you’d leave it idling for a few minutes while it warmed up (and stopped smoking), before applying any load.
Modern engines are much simpler – turn the key (or push the button) and they start. Instantly, every time. Without any smoke. And you can drive off pretty much immediately, without having to wait for them to warm up.
Modern boat engines no longer create clouds of fumes and generate far less noise and vibration. They have two other significant benefits: they consume considerably less fuel than their predecessors, and smaller (and lighter) engines generate the sort of power that previously required a bigger displacement.
Which is fantastic – until they don’t work any longer. You turn the key and get nothing – maybe a couple of beeps and a dreaded computer fault code on the gauge. This doesn’t actually tell you what is wrong.
Troubleshooting is now a standard sequence: check the battery, turn the engine master switch off and back on again. Like a desktop computer, the first step in troubleshooting is a reboot. If you’re lucky it clears the fault. If not you switch to the second approach – unplug and re-plug all the computer cables.
So many components on a modern engine are now directly controlled by a computer. How is it that a diesel now starts instantly? Because the computer senses the temperature, injects just the right amount of fuel into the engine at precisely the right time to initiate ignition. And then it automatically adjusts the amount and timing to keep her running as she warms up. But when the computer is uncooperative, nothing works.
Arguably, in the good old days things were simpler. A diesel engine needs fuel, air and a way to turn it over. With enough cranking it will eventually start. The petrol equivalent is a little more complex – it also requires a spark, of the right size and at precisely the right time. But for both a competent home mechanic with a few basic tools could do a good job of diagnosing the fault and correcting the issue.
Of course, this did require a degree of experience and competence with mechanical devices, a comprehensive set of tools and knowing the location of all the critical components on the engine. And invariably dirty hands and oil over the deck. Not so with a computer.
CODED MESSAGES
Manufacturers of modern engines seem to go out of their way to make it hard to diagnose a fault, providing codes rather than actual details. The engines often require proprietary computer interface cables, and it’s hard to make sense of the numeric code without an actual computer to plug in to it.
But there is a way to make sense of a computer code/fault that doesn’t clear – a workshop manual. Not the Owner’s Manual, but the detailed, technical manual that lists the fault codes and their causes.
This can take a bit of finding but thanks to Google these are available for just about every make and model of engine. Depending on the manufacturer, the manual may have quite detailed and helpful steps for troubleshooting and rectifying the problem, even showing you exactly where on the engine the offending component is. Print a copy and keep it on board!
Armed with this weighty document, when you suddenly get say, a ‘MID 164 PSID 95 FMI 2’ code, looking it up will identify it as a fault with the throttle lever not being detected properly. In the case of my Volvo Penta D4-260 engines, rectifying this is a simple process of re-calibrating the throttle lever positions.
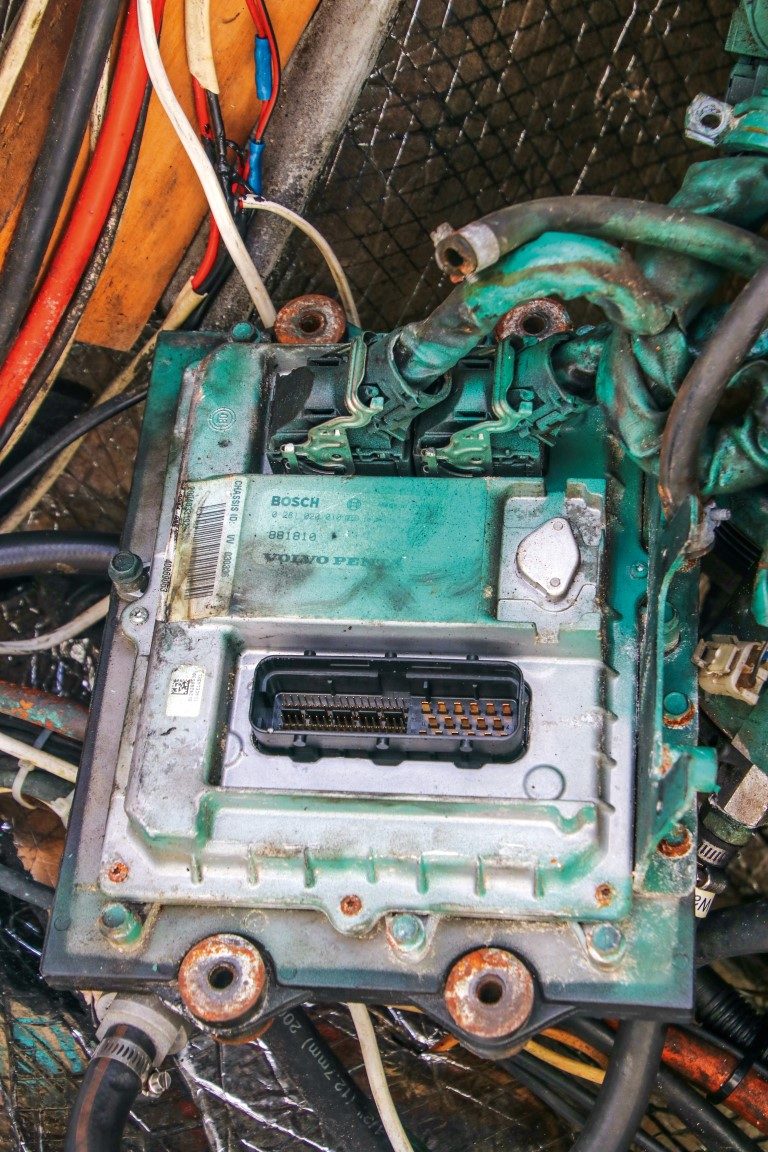
Previous faults have also been easy to pinpoint (fuel pressure sensor, water detected in fuel, and others) and although some are more complex to rectify the computer code at least identified the problem.
One downside of all these electronic sensors is that you cannot always tell if the device is faulty, or whether the sensor is telling you there’s another problem. In my case the fuel pressure fault turned out to be a faulty sensor, which required a replacement, while the water-in-fuel was a valid issue that I needed to clean.
In both cases – without the computer – I’d simply have been aware of the engine losing power, with no simple way of knowing what was causing that loss. The computer told me exactly what to investigate and where to find it.
Of course, computers themselves can also go wrong, and unfortunately you cannot just pop down to the local IT store and get a replacement. The modules are proprietary, often specific to the model of engine, and can be eyewateringly expensive.
They also require programming, which needs an authorised agent with the appropriate tools. And because they’re so model-specific they may not be stocked by the local agents, so there may be some lead time to get a replacement. Luckily, they don’t fail too often, since they are usually fully-sealed units, and are relatively easy to access and replace.
COMPUTER CONTROL
Most engines have at least two (sometimes three) elements to their computer control systems:
• ENGINE CONTROL UNIT (ECU, also called ECM)– is the module located on the engine itself. It controls the components such as the injectors, fuel pump, oil pressure, water temperature etc. It also receives inputs from the multitude of senders and sensors on the engine
• THE HEAD CONTROL UNIT (HCU) – usually located at the helm. This is the module that the electronic throttles, gauges and NMEA-2000 interfaces plug into
• POWERTRAIN CONTROL UNIT (PCU) – it communicates to both the HCU and ECU. Note that some engines integrate the PCU and ECU, while others have two separate components. The PCU often controls the gear shift, power steering (if fitted) and external sensors like the fuel tank level.
These units are generally joined by what is called a bus cable – basically a data cable that shares digital signals between them. Although the bus connectors are waterand dust-resistant, they may occasionally develop a poor connection. So unplugging and re-plugging a connector is a good troubleshooting tip, especially if the fault code translates to something about “communication failure”.
Although one of my engines recently experienced a complete PCU failure (which cost $4,000 to replace), I still wouldn’t consider reverting to the old mechanical engines originally installed in my boat.
My current engines (four-cylinder, 3.9-litre diesels) are each 150kg lighter than the previous six-cylinder 5.8-litre units, yet each develops 50 more horses. Although they have a slightly lower torque curve, a supercharger (in addition to a turbocharger) helps them get through that mid-rev range and the boat gets up to cruising speed without trouble.
And after installing them overall fuel economy improved by nearly 20%. This was a combination of the lower weight, causing the boat to sit slightly higher in the water (less drag), and the lower internal friction losses due to four rather than six cylinders.
But the main factor was undoubtedly the very precise control of the fuel injection process provided by the ECU. So almost no fuel exits unburned through the exhaust, and the power output is much closer to the theoretical maximum energy available per litre of fuel used.
Of course, all of this doesn’t stop me swearing whenever I get that dreaded beep at the helm. But I then remind myself that the computer code enables me to pinpoint the problem and prevent a minor issue becoming a major one later.
And overall, this means less time fixing major engine issues and more time on the water. BNZ