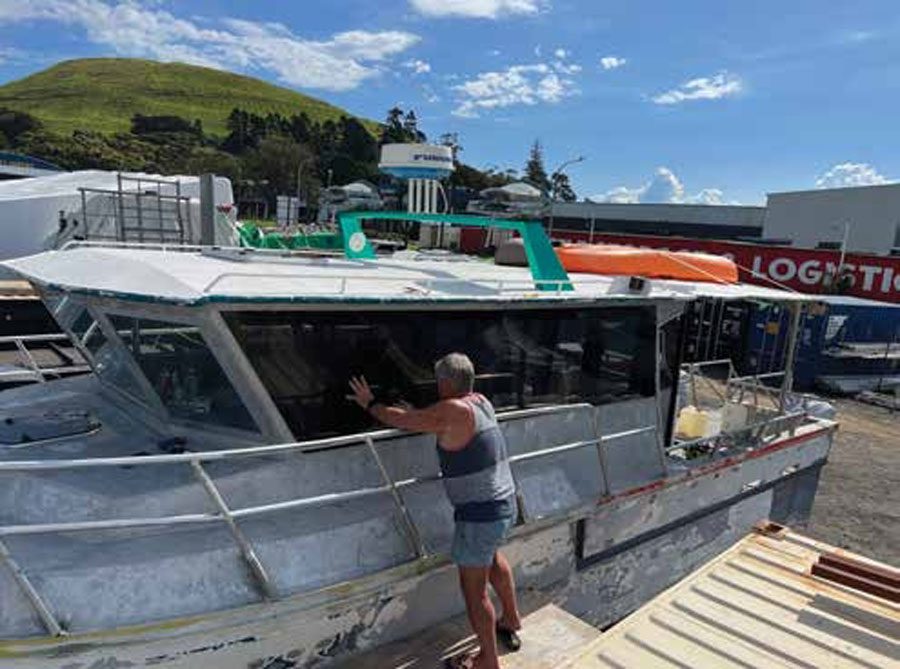
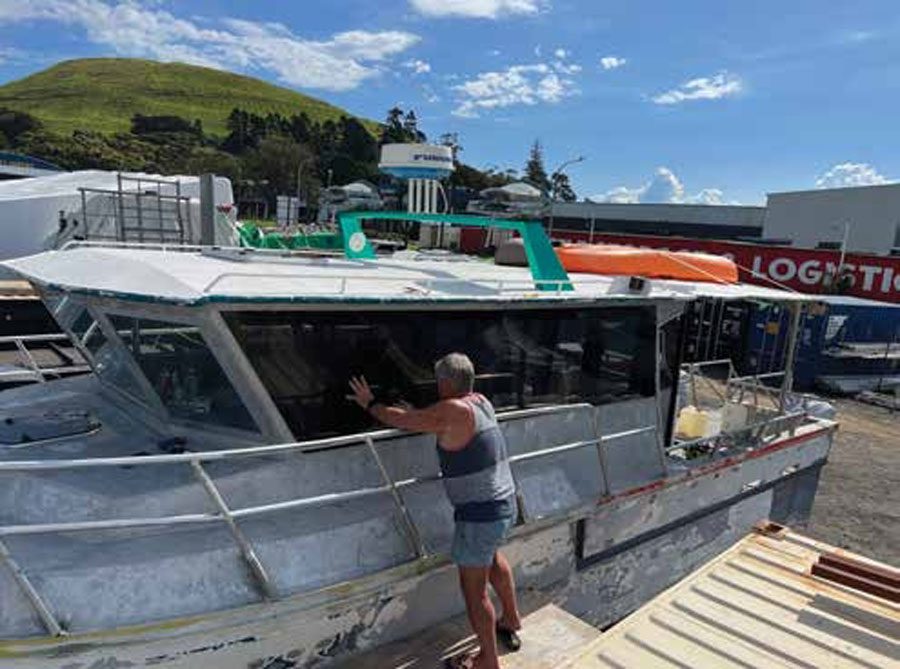
Last month we replaced the front windows of Divecat, using extruded aluminium window frames and the original toughened glass windowpanes held in by numerous small bolts and appropriate sealant. This closely matched the designer’s specifications and maintained the boat’s ‘workboat tough’ look. And the resulting windows are very strong indeed.
However, for the sides of the cabin we wanted something more stylish, newer, and much more extensive than the original design. During the post-salvage clean-up, we cut away some of the solid aluminium panels that made the cabin interior dark and gloomy. We will now fit windows running the entire length of the enclosed section of the boat. For this longer section, only tinted acrylic material made sense. Using this thin but ultrastrong plastic for the windows will produce a sleek look with a single black strip running the full length of the cabin exterior.
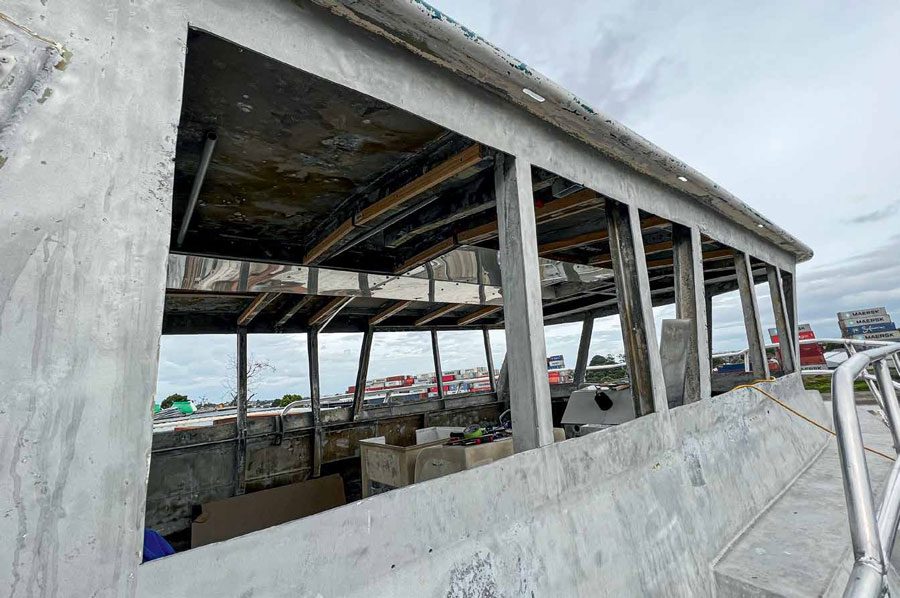
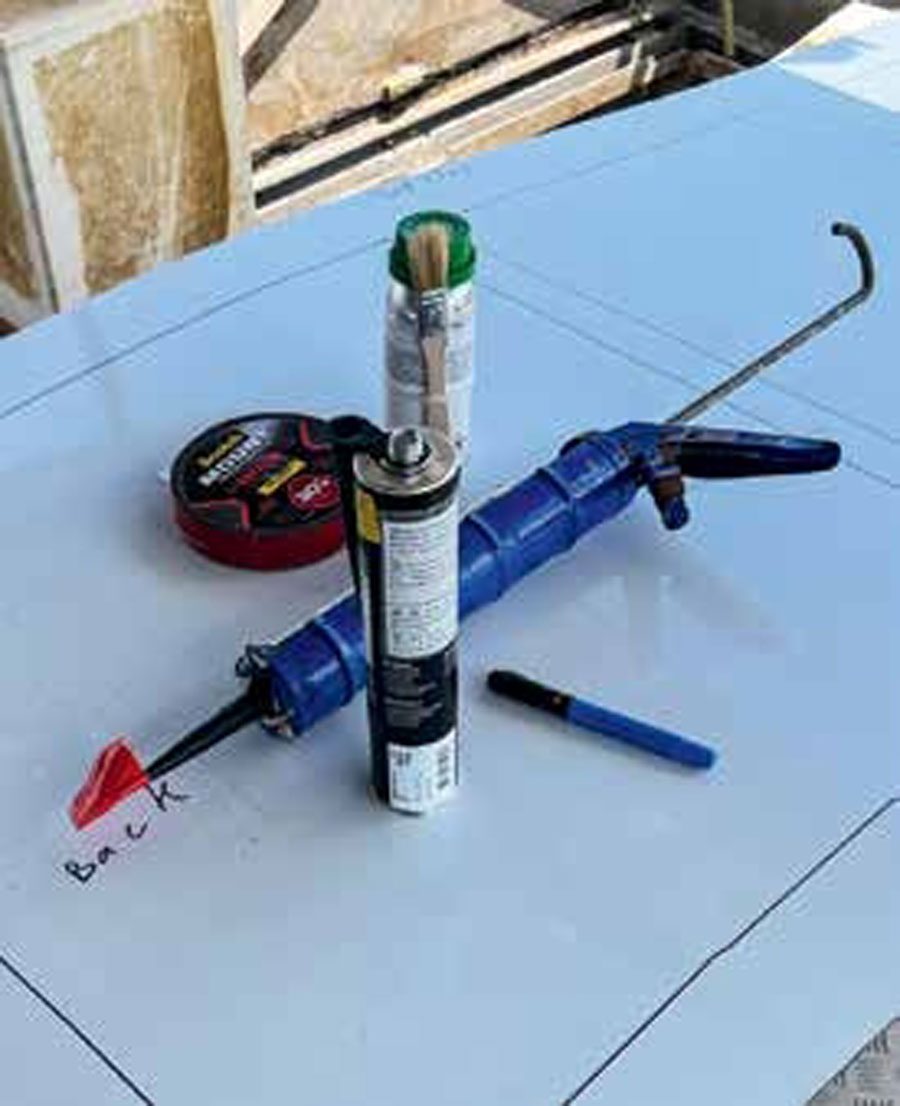
Well, not quite a single strip. Extra-long panels are only available on special order and are considerably more expensive than the standard 2.4m-long pieces (8-feet long by 4-feet wide in the old measurements). To reduce costs, and to make the pieces easier to manhandle, each of the 3.6m-long side windows is made up of two sections. These will have a thin join that will only be visible on close inspection. At 80cm in height, the new windows provide the skipper with 360° views from the helm, eliminating the considerable blind spots that existed before.
As we mentioned last month, modern adhesives and acrylic plastics mean that these windows could be bonded directly to the hull in a sleek frameless design that would also be strong and completely watertight. Also, because we would be using a flexible sealant to attach them, any imperfections on the aluminium panelling’s surface were automatically taken care of as long as the remaining metal was still solid. Hence no filling-and-fairing of the cabin walls was required, which simplified the installation process.
The acrylic is available in a variety of thicknesses, but after taking some advice, considering the size of the windows, and looking at a few other large launches with similar configurations, I decided that the 4.5mm thickness would be more than sufficient. In terms of impact-strength these are equivalent to the 10mm thick glass front windows, while being very much lighter and easier to work with. I ordered the panels cut-to-width from one of the several acrylic plastic suppliers in Auckland, and I chose the darker of the two grey tints that were available. This makes them look black from the outside but still provides plenty of light and good visibility from the inside looking out.
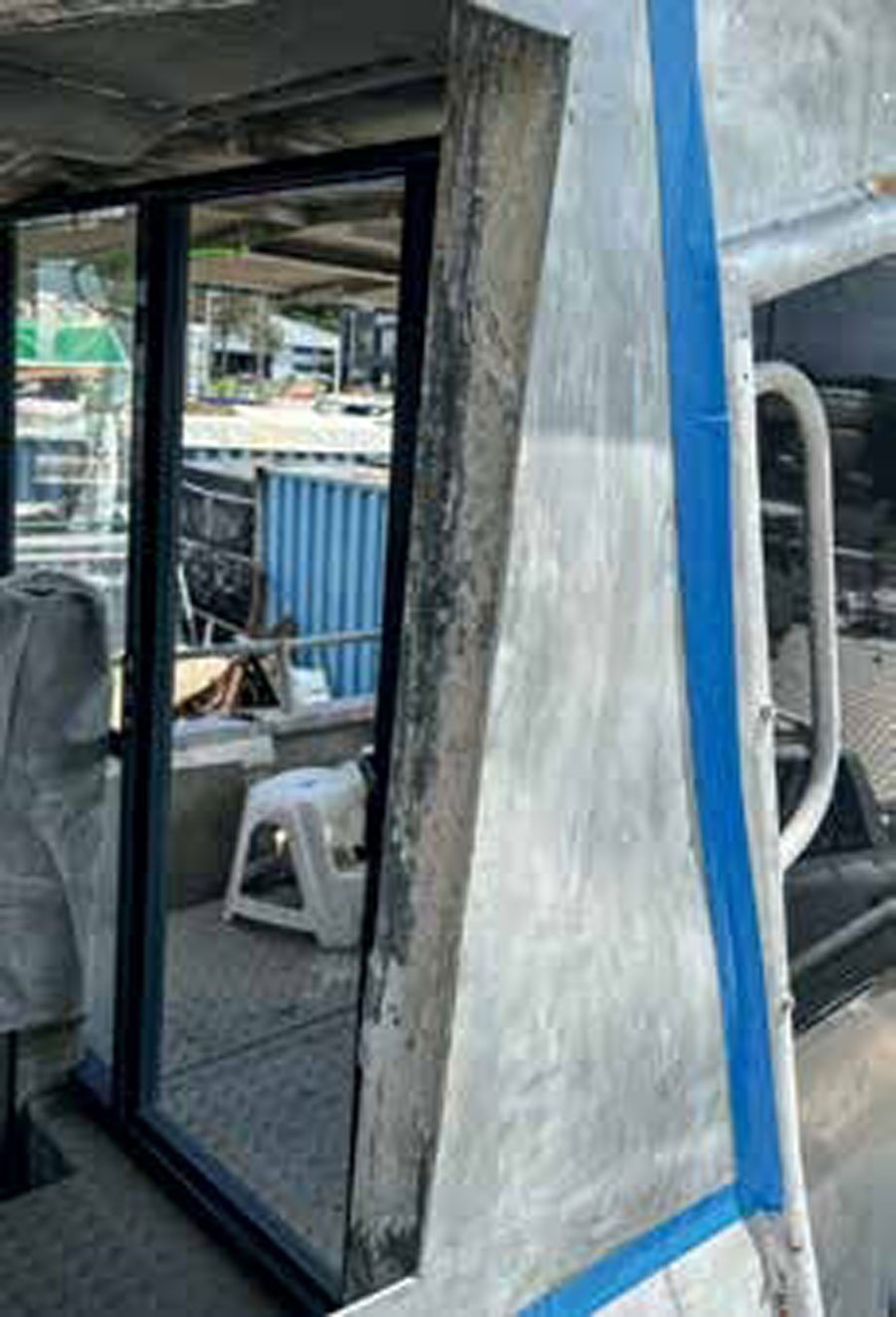
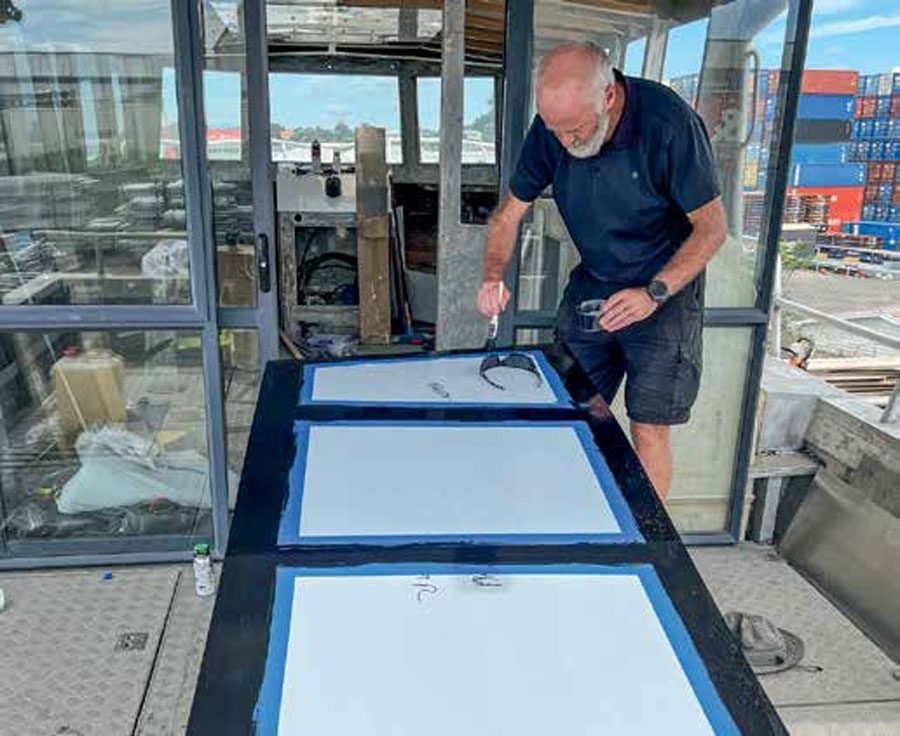
The plastic is supplied with a protective film on both sides, and this is retained until they are ready to be installed. Using a very fine-tooth saw blade on a circular saw I first cut the correct angle to match the slope of the cabin side. The edges were then carefully sanded and smoothed off, ready for installation.
And this is where it gets slightly tricky. There are several compounds specifically designed for installing windows, such as Sikaflex 552AT. Similar products are available from Dow, 3M and Meicon. Notice these is not just black silicone, but rather a polymer adhesive specifically formulated for sticking to acrylic and common substrates such as fibreglass gelcoat and aluminium. All these compounds require a primer to first be applied to the hull and the inside of the window, which aids adhesion and prevents UV damage to the sealant.
Each surface required a different primer, which are very thin liquids that are brushed onto a masked off area. The acrylic primer (Sika 209 Primer) is opaque black while the aluminium one (Sika MultiPrimer Marine) is clear. On the inside of the window sheets, the protective film needed to be peeled back from the edges of the acrylic before masking-off with tape, then lightly scuffing the acrylic, and finally applying the primer.
The outside of the cabin was easier as the surface was already roughened from the sand blasting previously, so it was just mask off and apply.
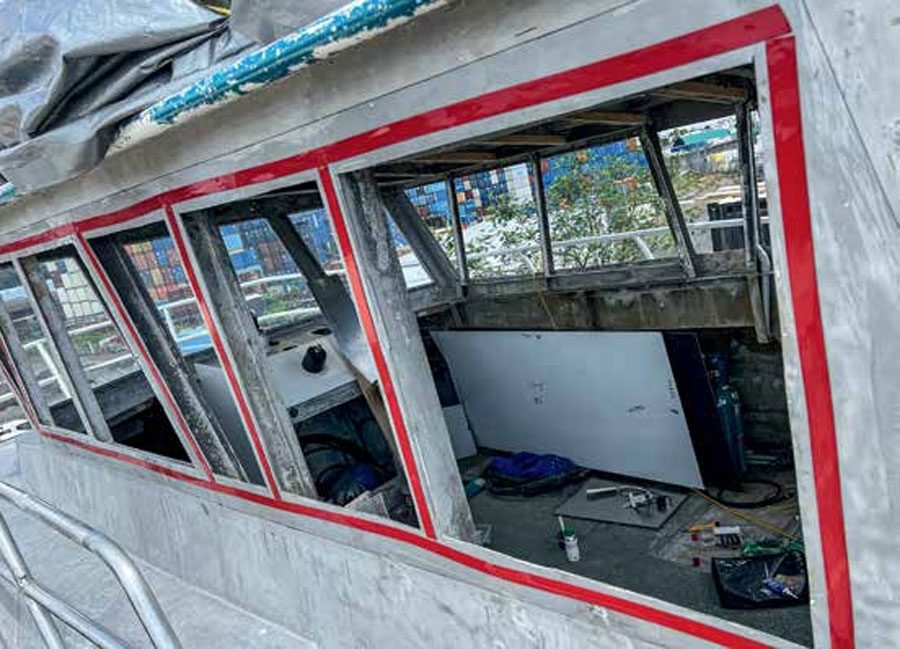
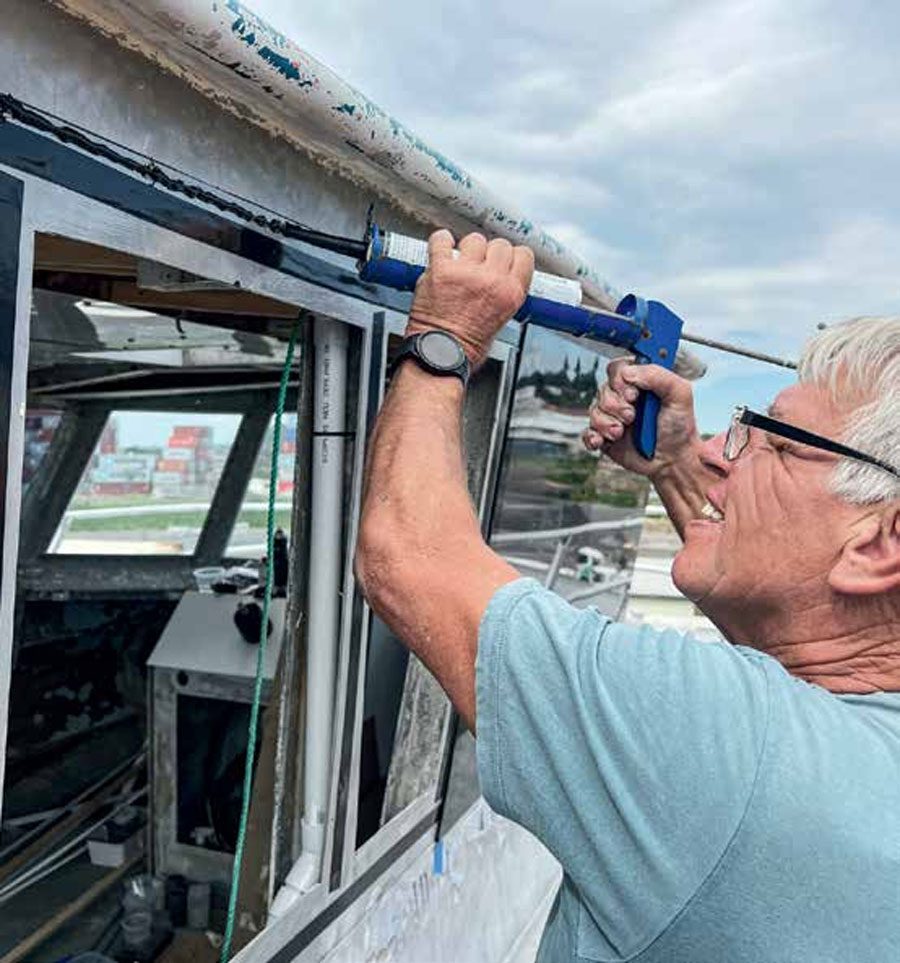
For holding the windows in place, we utilised well-known industry ‘hack’. 3M makes a double-sided tape called VHB (Very High Bond), and a strip of this is placed all along the centre of the primed area of the window. This will hold the window securely in place, and in fact provides the primary source of adhesion for the windows. An added benefit is that it creates an even gap between the window and cabin side, so the final sealant edge is the same thickness all around. Since the tape is black and hidden behind the black primer, it is invisible. The only downside of this system is that there are no second chances – the window must be in exactly the right spot before it is pressed into place, as the VHB tape has instant grab and cannot be pulled off and repositioned!
Once the primer had dried, we positioned a strip of the tape down the middle of the primed area on the cabin side. A thick but more-or-less even bead of sealant was then applied close to the edge of where the window would sit, with a similar bead close to the internal edges where the window will be seen from inside the cabin. Note this does not need to be right at the edge as it is merely a secondary water barrier, and we applied it to the cabin sides rather than the acrylic sheet so we would not accidentally smear it as we manhandled the window into place.
Once ready the window would need to be very carefully positioned, and then pressed into place where the VHB tape would hold it securely. This is not a job to do single-handed, and I called on my buddy Ron to help me get them positioned correctly. We also chose a day without any significant wind, to make it easier to manipulate the long pieces of flexible plastic.
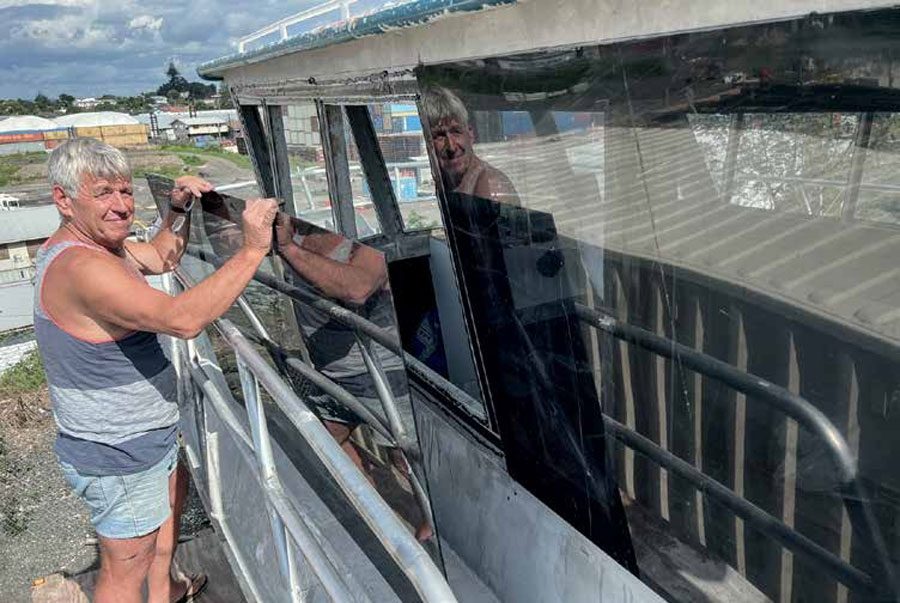
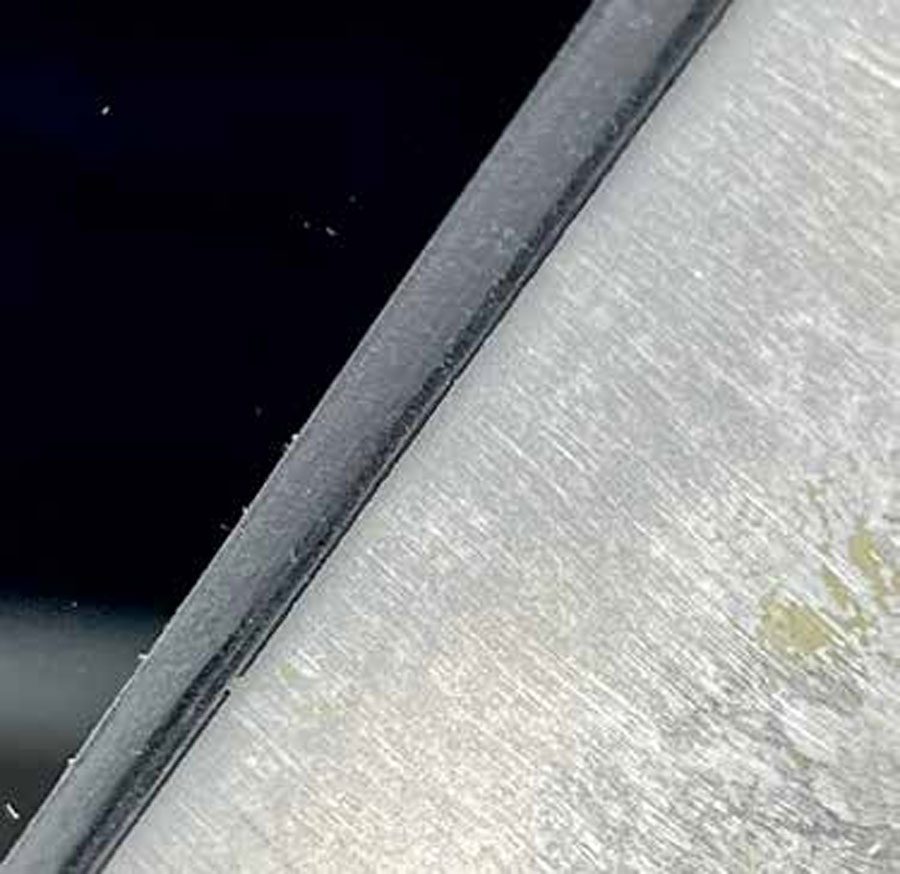
Once we had the acrylic panel in the right spot, we applied pressure all along the invisible line of VHB tape, and it was instantly stuck very tightly. From the inside of the cabin, we peeled the remainder of the white protective film off the acrylic so we could get a feel for the final view, and it is as good as I had hoped. The outside still has a clear protective film, which we will leave in place until just before we relaunch Divecat.
The final bead of sealant around the edge of the window can be done immediately or at a later stage. Once again, masking it up properly is the secret of success, and it is then a simple matter of using a caulking gun to neatly run a bead all around the window. It is important to make sure the sealant injects into the gap as well as along the edge. A rubber ‘finger’ can be used to smooth off the edges rather than your real finger, and after a short period of time the masking tape can be removed. It is best to do this once the sealant starts to ‘skin’ but before it fully sets, so that it leaves a neat edge without smearing the freshly applied sealant. Isopropyl alcohol is used for a final clean-up, rubbing off any wayward streaks of sealant.
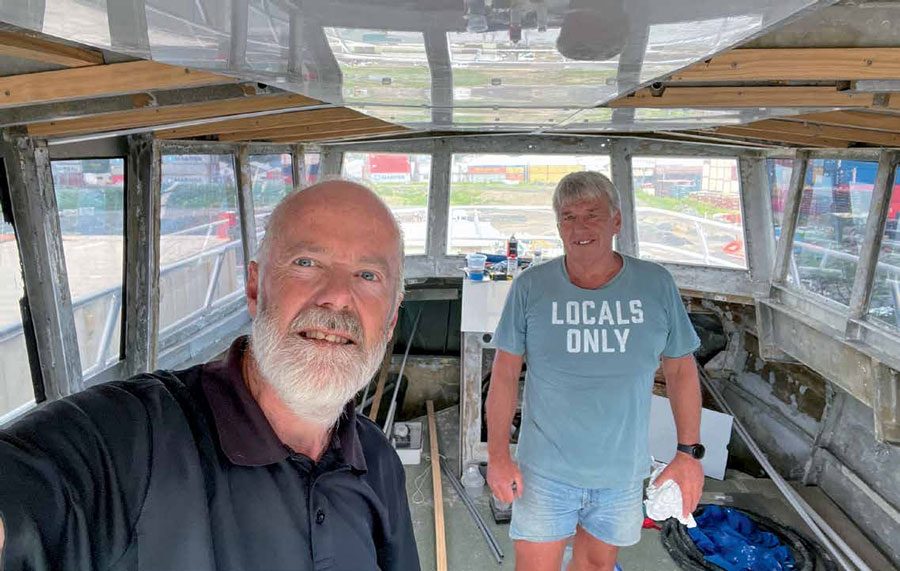
Fitting completely new windows like this was not cheap. The acrylic panels cost around $250 each, and we needed four sheets. The Sikaflex 552AT is around $50 per tube from most marine chandlers, and we used four tubes. Sika 209 Primer and Sika MultiPrimer Marine are $60 each from those same sources, and we used a can of each. The 3M VHB tape is nearly $50 per roll from the big-chain hardware stores, and we required three rolls. So altogether the four window panels cost us almost $1500 for materials, not a bad cost considering the sheer size of the windows we fitted. And they should be good for the next 15 years at least.
Now the cabin of the boat is very nearly weather-tight, with only a couple of flashings around the rear ranch slider still needed to fully enclose it. I think a ‘roof shout’ party may be coming up once she is watertight again! BNZ