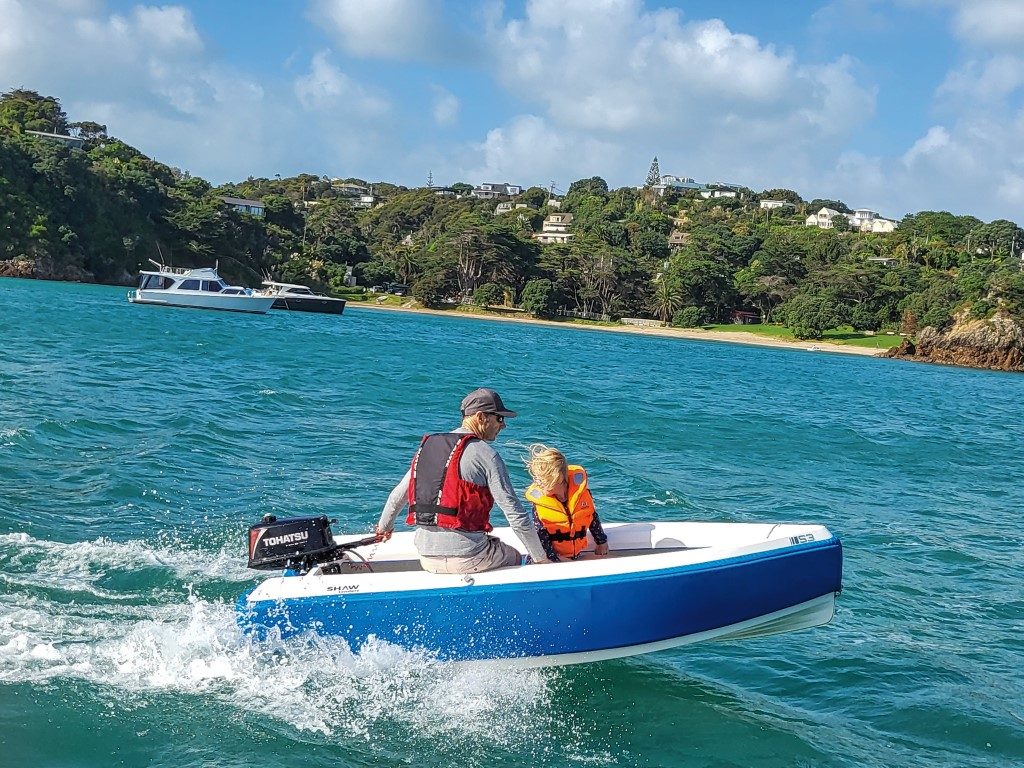
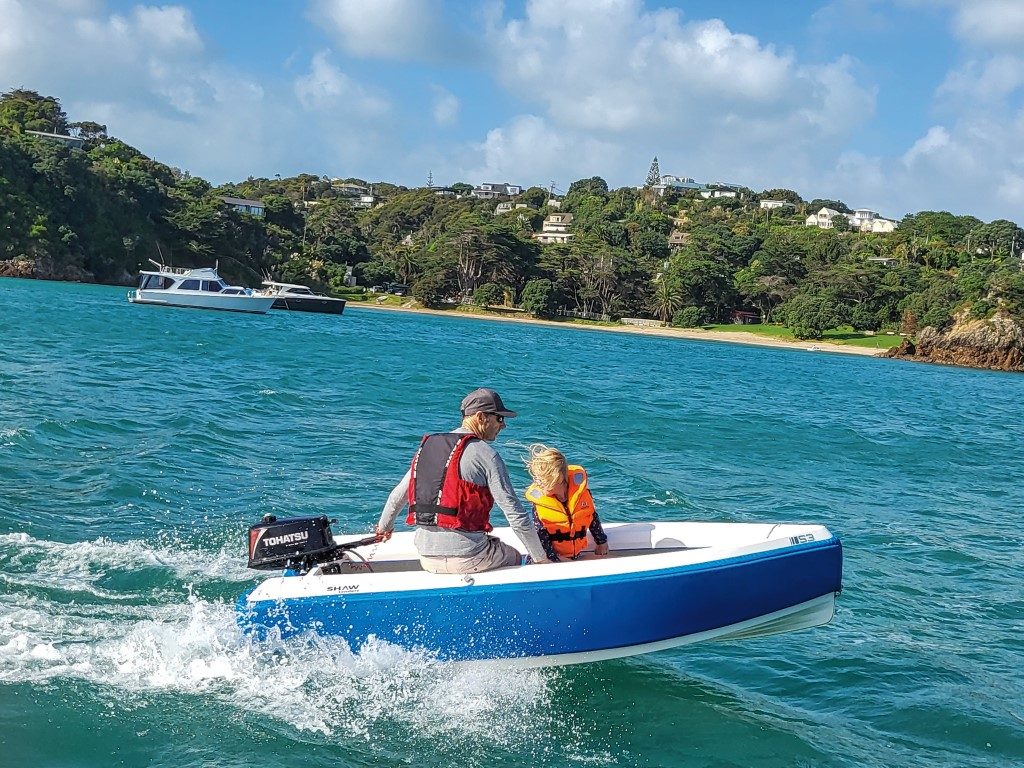
All hail the cruising tender! We ask a lot of these valiant little vessels. Tenders must reliably ferry people, pets and provisions to and from shore in just about any weather.
They must row well, tow happily and jump onto a plane easily. They must get us and our picnic and our watertoys to the beach or out to the reef on diving, fishing or surfing excursions. They must transport our families up rivers and across bays, and be light enough to be carried up the beach and lifted onto the mothership. And they must be powerful enough to help us get a second anchor and rode up to windward in a blow. Our tenders must be stable, unsinkable, fast, safe, comfortable, throw a minimum of spray and need little upkeep. Fortunately, in recent years a lot of Kiwi innovation has been applied to the humble cruising tender, in its many inflatable and hard variations.
The newest entry in the field is the Shaw S3 Tender, a rigid 2.9m planing tender, the brainchild of Auckland-based yacht designer Rob Shaw. Shaw is best known for his high-performance keelers, foiling sportboats, and canting keelers, along with powercats and chase boats. Why and how did he create a cruising tender?
“I have spent years cruising around the New Zealand coastline,” says Shaw. “Through this I have experienced a broad range of tenders of various designs and construction types. For a long time, I have been working on the idea of a hard tender that could combine the benefits of a traditional lightweight plywood dinghy with the benefits of an inflatable. More specifically, I wanted to blend the light weight and efficiency of the traditional tender with the stability and soft exterior of an inflatable, and in the process make the tender more robust and beach friendly.
“The design process I applied in the development of the S3 was similar to any design project I take on. It’s a challenge when you are your own client, though, so I gathered input from other people who have a lot of experience in various tenders to get their perspective and learn what they were looking for in a tender.
“From there I prioritised a list of objectives, then got underway developing a series of 3D CAD (computer) models to experiment with different hull forms, deck shapes, and layouts. 3D modelling enables accurate refinement of the geometry, performance, and stability analysis, and then CNC machining of the tooling to build the moulds. 2D CAD drawings show the final specification and construction details. This is a level of accuracy, analysis and refinement that is probably unusual on a boat of this size, and reflects the process I would use to design a race boat.”
Shaw notes that the advanced level of design and analysis eliminated the need to build and test a prototype; Shaw went directly to building a mould and the first production boat.
“The construction specifications for the S3 were a collaborative effort between myself, Matt Gottard from MG Composites, and engineering analysis from Pete Lawson of Hauraki Design Consultancy. The objective was to achieve a light yet durable tender. These are two attributes which are often in conflict, especially in a small boat that will regularly come ashore or be stored on a larger boat. This led towards the need for full carbon construction. The boatbuilding process includes Bill Barry from Covers and Canvas, who helped with the development of the trackless fender system, and Performance Boatbuilding in Cambridge, who build the boats in infused carbon to a high standard.
“From there, one of the solutions we applied was to utilise a monolithic carbon hull shell in high load or impact areas, a construction method seen more commonly in some offshore race yachts. This was a great option for the hull bottom of the S3, to prevent impact dents, inside and out. This issue can be hard to avoid in small, light boats built with light laminates over a foam core. A combination of design and engineering optimisation and the use of resin infusion in the construction process made it possible to utilise this monolithic construction method on the bottom to gain a strong, impact resistant yet light structure.”
Flatter surfaces such as the topsides, decks, and built-in seat have a foam core for panel stiffness, light weight and added buoyancy. All exterior surfaces are finished with gelcoat. The key to the boat’s ability to withstand hard knocks from a stony landing is the carbon-infused monolithic hull bottom.
“The advantage of carbon is the significant increase in stiffness and overall strength it provides, without adding weight. It enables us to build a tender that is both light and strong. You get the advantage of the boat being lightweight without becoming fragile. Carbon fabrics infuse nicely, and this process ensures consistent, high-quality void-free laminates.”
The main drawback of carbon fibre laminates is increased cost. This is largely offset, Shaw says, by producing a high-quality product that will be light and robust, and last a long time.
“The hull form of the S3 is optimised for early planing and high stability. The relatively fine entry provides a soft
ride and the multiple spray strakes deflect the spray, keeping the boat dry when underway. The design ensures that the boat performs well with either a light payload or when carrying a full load of people or supplies. Testing with a range of electric and petrol outboards revealed that the S3 performs equally well with either propulsion option and can easily plane with minimum power.”
Two aspects of design were targeted: creating a tender light enough for one person to pull up the beach was a high priority, without the boat being fragile. The other component was to design an efficient boat that can achieve high performance on the water with a small engine.
“One of the greatest weight savings is achieved through the ability to run a smaller horsepower engine and still get on the plane,” notes Shaw. “This is also a very favourable attribute if you are running electric propulsion. Electric systems are considerably more limited by battery capacity, weight, and range, and therefore benefit considerably from being paired with an efficient tender.”
The S3 features wide, flat side-decks with a bevel at the gunwale, which makes it comfortable to sit on and easy to step on and off. It also creates storage space underneath, along each side. The gunwale bevel proves ample space to attach oars or other accessories, such as rod holders. The tender has a quick-release fender skin system, which can be removed and reattached in a few minutes. You can clean beneath it, store it separately away from sunlight, or refresh your tender with a new colour or graphics. The soft fender skin means you can come alongside other boats without damaging either vessel.
Shaw has more tenders in the pipeline. Using the same design process, and working in a similar geometry of the deck and the gunwale bevel, he also drew the twin-hulled 3.9m OneTender 38 https://onetenders.com/ for One Tenders.
“Creating the S3 has been a really interesting process, thinking about what I and other boaties would really like in a tender, and what are its most important attributes,” says Shaw. “It’s certainly been a great boat for our family.”
That’s it. When a new tender proves to be not only innovative but fun – a hit with kids and not-so-young kids – that may be the ultimate proof of concept.