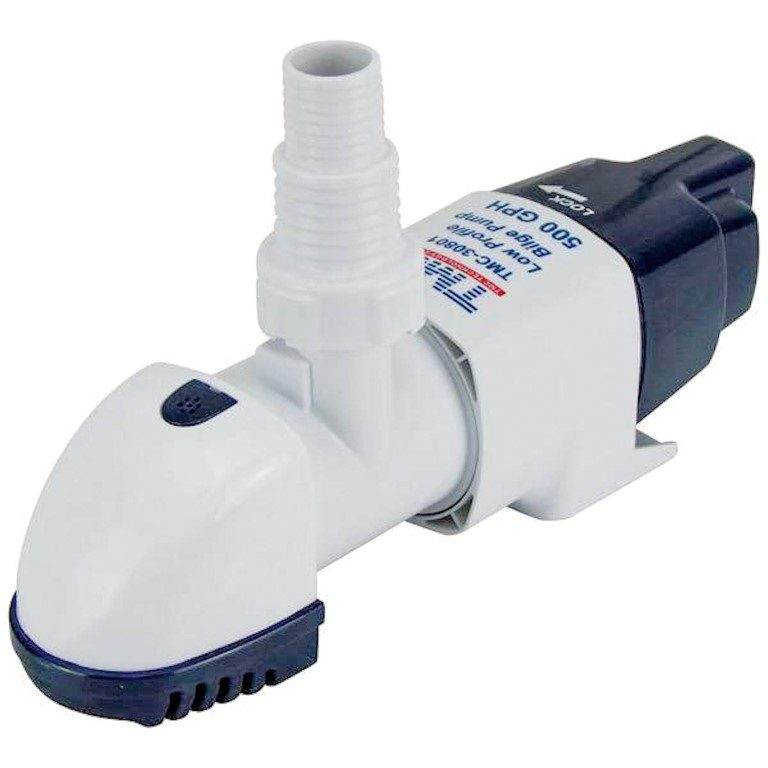
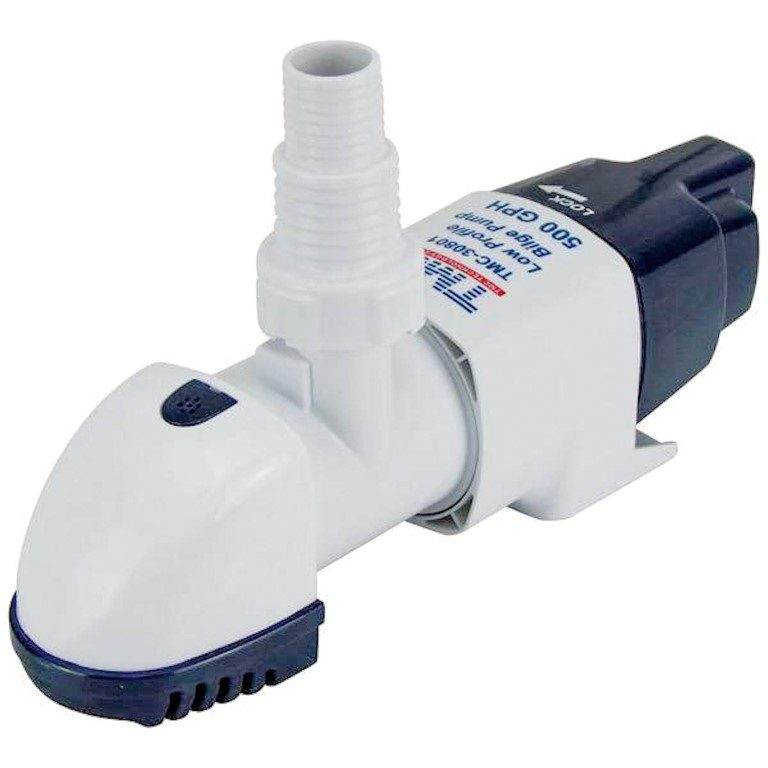
A fundamental part of every vessel’s operational safety, a bilge pump’s capacity and installation must be carefully considered. Story and pictures by Norman Holtzhausen.
Boats usually work best on the principle that water remains outside the hull. But inevitably, some water will make its way on board and migrate to the lowest point in the bilge. That area is usually hard to access and can get quite mucky over time as any contaminants also work their way down there.
These include oil, diesel, fish blood, scales, dust, mud and barnacles – which means the bilge pump must be of a design that resists clogging. Fortunately, today we have some very good designs, with pumps that have only one moving part – the impeller. This component is encased in a fully-sealed body that’s completely impervious to water and, unless it is cracked or physically damaged there is nothing in the pump body to wear out.
The impeller itself is encased in a strainer at the bottom of the pump, and the entire unit sits in the lowest point of the bilge. The spinning impeller sucks up almost all the water, usually leaving just under a centimetre remaining. An automatic switch, usually encased in a floating bail arm with sealed contacts inside, turns the pump on as soon as there is enough water to lift the floating arm.
A float switch usually turns off at a lower water level than is required to turn it on, to prevent ‘cycling’. This can happen once the pump turns off, as any water still in the outlet hose will slump back down into the bilge, raising the water level again.
If the switch is overly-sensitive it could repeatedly turn on/ off as this water is partly pumped out and returns. Instead, most units will keep pumping for a short period past the trigger level to get rid of as much water as possible and ensure the remaining water does not trigger the switch again.
The bilge pump is the one accessory on a boat that should be wired directly to the house battery, and not go through the isolator switch. This is especially important on moored boats that may be left unattended for some time. You’d rather get back to your floating boat (with a flat battery), than find it sunk because the bilge pump couldn’t deal with water ingress.
Another requirement on commercial vessels (and a good idea on recreational boats) is to have an audible alarm that sounds when the bilge pump kicks in. This lets you know instantly when the bilge pump starts dealing with some water, which may be the first indication that you have a leak. Although the noise may be annoying it’s better than not realising you have a problem until it’s become serious.
HOW MUCH VOLUME?
A bilge pump’s flow rate might look impressive but a serious hull breach can overwhelm even the biggest pump. A 2.5cm hole through the hull (say from a sheared through-hull fitting) will allow around 1,500 litres of water per hour (350GPH) into the boat when it is just 3cm below the surface. Move that same hole to 30cm below the surface and the increased pressure will force in around 4,000 litres per hour (1,100GPH) of water.
And that same hole at a metre depth will result in nearly 12,000 litres per hour (3,000GPH) gushing in. So with a major hull breach the most important thing is to be alerted to it and immediately take action to at least slow the rate of water ingress. Even a rag jammed tightly into a hole can greatly reduce the flow and allow the bilge pump to cope until you get to safety.
PRESSURE VS VOLUME
A bilge pump’s most important feature is volume – to move the water as quickly as possible. All pumps specify their flow rate in GPH (gallons per hour), using the American gallon of 3.8 litres. The capacity of even the smallest bilge pumps is quite astonishing, with 500GPH being the starting point of most manufacturers’ range.
This equates to nearly 2,000 litres per hour, or 30 litres per minute. Larger pumps will double or quadruple this, and even a very fit person bailing by hand could not match this flow for more than a few minutes. So a functioning bilge pump should be an absolute priority in even the smallest of boats.
But the centrifugal impeller design of most bilge pumps means that while it can move a lot of water, it can’t necessarily lift it. This is because the pump output pressure is very low – and the higher it has to lift the greater the ‘weight’ of water in the outlet pipe. This means that the higher the pump outlet is in relation to the intake, the lower the pumping rate.
One of the most popular brands of pump available in New Zealand has an effective capacity that drops to just 50% of the rated flow with just six feet of head, which is not uncommon in a deep-keel vessel like a yacht. Some imported budget models have an even greater drop-off due to lower output pressure.
The practical implication is that the outlet of your bilge pump should be as low as is safely possible: high enough that there is no possibility of water coming in through the outlet in bad weather, but low enough that the bilge pump does not have extra work.
Of course, this has additional issues with boats that heel: if the outlet’s too low, it could be below water when the boat’s heeling and allow water to enter through that very outlet. The outlet position should be selected carefully to prevent this, and a non-return valve incorporated into the outlet pipe to prevent water coming the wrong way.
Also note that bilge pumps are quite useless as washdown pumps or general pumps. Low pressure and the strainer inlet on the bottom means they cannot suck water from a fitting nor can they deliver very sufficient water pressure for washdown purposes.
Specialist pumps are needed for these activities.
TYPES OF PUMPS
Generally, there are three bilge pump styles: CYLINDRICAL
These look like a small round canister and have the strainer on the bottom. This clips off and is usually fixed to the bilge floor. The pump body then clips back into the strainer. This style has no integrated switch, and a separate bail arm or electronic switch is required to control the pump. This style comes in the biggest sizes – 3,000 GPH units and even bigger are not uncommon
SELF-CONTAINED
These are smaller and incorporate the float switch within the body of the pump. They are usually an oblong shape as the switch mechanism is on the one side. The simplest design to install, it doesn’t need a separate float switch to be wired. The size range is more limited compared to the cylindrical models
AUTOMATIC LOW-PROFILE PUMPS These models have the motor part lying on its side, which limits the size and capacity of the motor. But they have a much lower profile, and are suitable for installing in areas with very limited space such as under the sump of an inboard engine.
All automatic pumps come with three wires: one negative and two positive connections. The negative and float switch positive should be connected directly to the battery supply, preferably also incorporating an audible alarm unit. The other positive wire is for a manual over-ride switch, which lets you turn on the bilge pump even if there is insufficient water to activate the float switch.
This is useful when you want to remove the maximum amount of water from the bilge, since the float switch will turn off once the water drops below a certain level. But it should not be run for more than a minute or so, as there is a risk of burning out the motor.